09 Apr 2015

Besides 3D printing hands, we have several other projects going on down at the io-estate and the Maker Station. I'm pretty excited to start making some progress on our entry into this season's Power Racing Series race at the Atlanta MakerFaire.
While the gauntlet and palm parts were printing last weekend, I mocked up the car's frame in PVC. A couple of days ago I procured some 1/2" steel tubing from Metals Supermarket... which was not as super as I had hoped. However, it was super convenient in that I placed the order online, and was able to pick it up later that day. I was hoping to find a big warehouse type of supermarket where I could wander through and see steel and cutting machines because steel, but instead it was just a small store front and the guy went back into the employees only warehouse to grab my order. The entire transaction took all of two minutes, super convenient.
Also the guy behind the counter sound German or Eastern European. He frowned when he saw me because it was 5:05pm when I arrived and he promptly informed me that they were closed. "But", I replied, "it's just a tiny order, already paid for... just 4 pieces of 0.5" x 6' square tube". He frowned, but went back and got it.
The transaction made me chuckle. A couple days ago I read this fanboy answer on Quora about mechanical engineering school in Germany, and here I was at Metal Supermarket of Marietta getting the evil eye from a German metal salesman.
I'm hoping to get down to the Station this weekend to cut and melt some steel into the intended frame.
Against everyone at the Station's better judgement, I elected to go with 1/2" square tube because, weight. If it doesn't hold up, we'll just fix it and reinforce it.

References:
If you liked this post, you can
tweet it to your followers
or
follow me on Twitter @tanjuB!
09 Apr 2015

Procuring hardware for the e-Nable hands is turning out to require way more effort than the actual printing. Yesterday I spent more than a half hour at Michael's craft store assessing all the options for elastic and tension cords for the finger actuation that I completely forgot to get the needed velcro.
Similarly, I tried 3 different local medical pharmacies for the medical grade foam and came up empty handed.
And then after going to Lowes hardware store twice and accidentally buying 3/8" long binding post screws instead of 1/4" long, I got tired of going and decided to trim to length.
The screws are too small to hold to take off 1/8" so I designed and printed this little jig sized for the post diameter. With care it can also be used to trim the screws.
Aluminum screws cut fast, in less than a minute.
This was my major accomplishment for the day.
You can download a copy of it and print your own Jig
If you liked this post, you can
tweet it to your followers
or
follow me on Twitter @tanjuB!
08 Apr 2015

More Progress
Having success printing out the cyborg beast hand, but it is turning out to be more work than the raptor hand. It turns out that the handomatic web-app doesn't necessarily contain the latest design available. Actually not sure what the latest design is, but there several variations out there. The design available on the handomatic doesn't contain tensioning block/system on the gauntlet. I found some comments on eNable's google+ page mentioning that it is supposed to use a commercial ski boot type of tensioner, but I couldn't find any details about it and frankly didn't feel like scouring the interwebz to try to figure it out.
Oddly enough, I did feel like spending time trying to add a tension block to the existing gauntlet that we have already printed. This also turned into a protracted exercise, taking many hours and a couple of iterations. Much longer than I cared for. In the end, I've got something that seems like it will work, but for the next iteration I will try out the Frankie Flood gauntlet design recommend by 3DUNIVERSE.
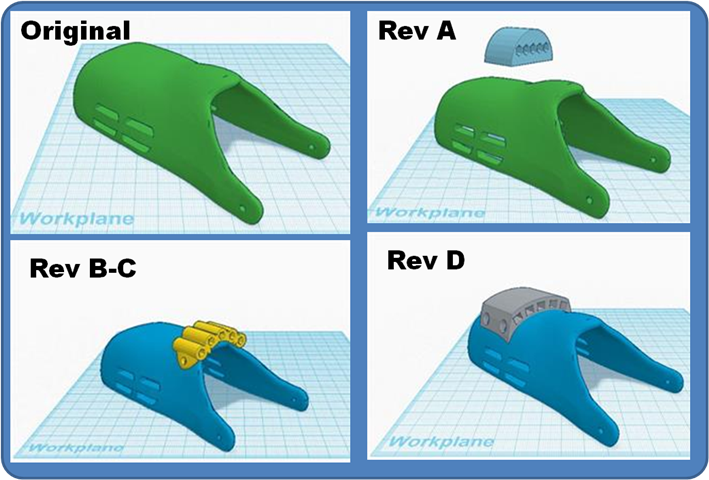

In addition to lack of tensioner, the cyborg beast hand uses Chicago screws for all the connections. Since the models is scaled, all the holes end up scaled and require being drilled out to accommodate the screws. I also need to shorten the post for the knuckles by 1/4" as standard off the shelf lengths are either just barely too short... or too long.
TLDR
Planning to stick to printing just raptor hands for the next opportunities that come up. They are simply just easier and faster to assemble.
My main goal in doing all this is that I hope to inspire the kids receiving these hands to know that they could develop the skills to print out and even design hands on their own. Really to empower and inspire them to be able to this on their own. With that in mind, I can print them their first raptor hand, and if they want a different design, we can teach them how to print their own. It's literally about enabling their future... www.enablingthefuture.org
06 Apr 2015

Making Progress
We had good success printing out the raptor hand. We are liking this design better than the cyborg-beast because the connecting pins are part of the design and are printed along with the rest of the other parts. It makes assembly more productive and satisfying to see it all come together so fast, vs having to size holes and bolting for cyborg beast. In the pic, the cyborg beast is sitting on the table waiting on hardware.
05 Apr 2015

A brief summary of how I became involved with 3D printing prosthetic hands with enablingthefuture.org
Sometime in 2014, my distant friend Kit Coleman shared a post about the e-Nable organization on my facebook feed. I had met Kit on the soccer field, our kids played together and for a season or two, we coached the boys together. But, after a couple of seasons they gave up on soccer and we didn't stay in touch other than the facebook connection. (Side note... why the hell is it impossible to search my own facebook timeline???)
Anyways, I was intrigued at putting my printer to good use and registered right away. And then. I don't recall that anything happened,
I never heard anything from them, other than occasionally getting spammy invites to google hang outs that I always ignored as I was easily sidetracked to look into it any further.
I did however casually keep an eye on the google hang-outs subject lines and knew that they were developing a hand-o-matic software to streamline getting the needed measurements to size the prosthetic for the individual in need.
Since not hearing a reply from eNable and not personally knowing anyone in need, I decided not to actively pursue finding someone. I was already too busy, plus printing hands seemed hard, and I was also afraid of the risk of getting someone's hopes up and not being able to deliver or do it right or cause some kind of damage from a medical liability standpoint.
So fast forward 8 months and I get invited to sit on a panel about starting makerspaces for educators and schools being held at the Atlanta Science Festival. The session was at GA Tech Invention Studio.
A teacher comes up to me and talks about wanting to get hands printed because she had TWO ten year old kids in the same class in need. I was like wow. So I recounted how I didn't know much other than e-Nable was out there and that they were making the hand-o-matic software. We exchanged emails and I forwarded her the link to hand-o-matic.
Two days later she replied with .stl files for printing, asking if I new anyone that could print them. I, of course, had to give it a try. I was pleasantly surprised to learn that the great folks at e-Nable had specifically designed the hands to be printed on FDM/FFF consumer grade printers. So after successfully printing a couple of phalanges, we were off and set on printing hands for these two kids (initially known as ProjectA and ProjectB).
My intention is to post each project separately to github repositories with details posted to their respective project pages. This main blog will host general updates.
Here is my initial tweet following success with the first phalanges.

If you liked this post, you can
tweet it to your followers
or
follow me on Twitter @tanjuB!